SAFETY & OCCUPATIONAL HEALTH
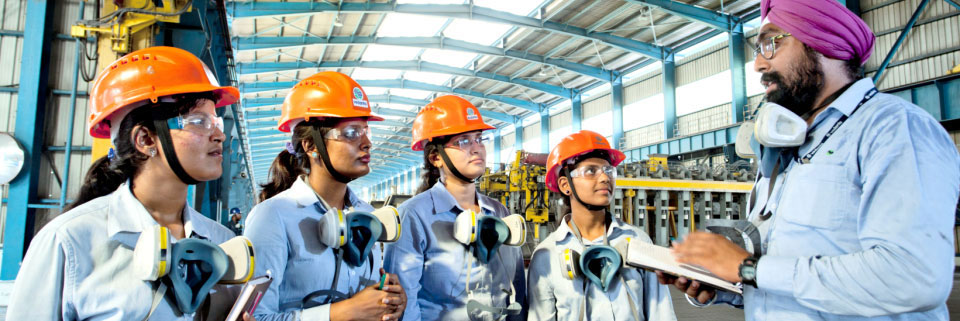
As a natural resources organisation, human capital is at the core of our business. Our employees are key to our success and sustainability. Their safety and well-being is our prime responsibility.
We work in remote locations and are aware of the many occupational risks inherent to our industry. We remain committed to an injury-free, illness-free and healthy workplace. Safety and well-being of our employees is an integral part of our decision making and the top priority in whatever projects we undertake.
Our health and safety approach is guided by Group Safety Standard which applies to all Vedanta business units and managed operations.
STRICT ADHERENCE
TO OUR SAFETY
PERFORMANCE STANDARDS
AND AN ADOPTION OF
ZERO-TOLERANCE TOWARDS
SAFETY LAPSES HAS BEEN
OUR PRIME FOCUS IN THE
REPORTING YEAR.
SAFETY PERFORMANCE HIGHLIGHTS
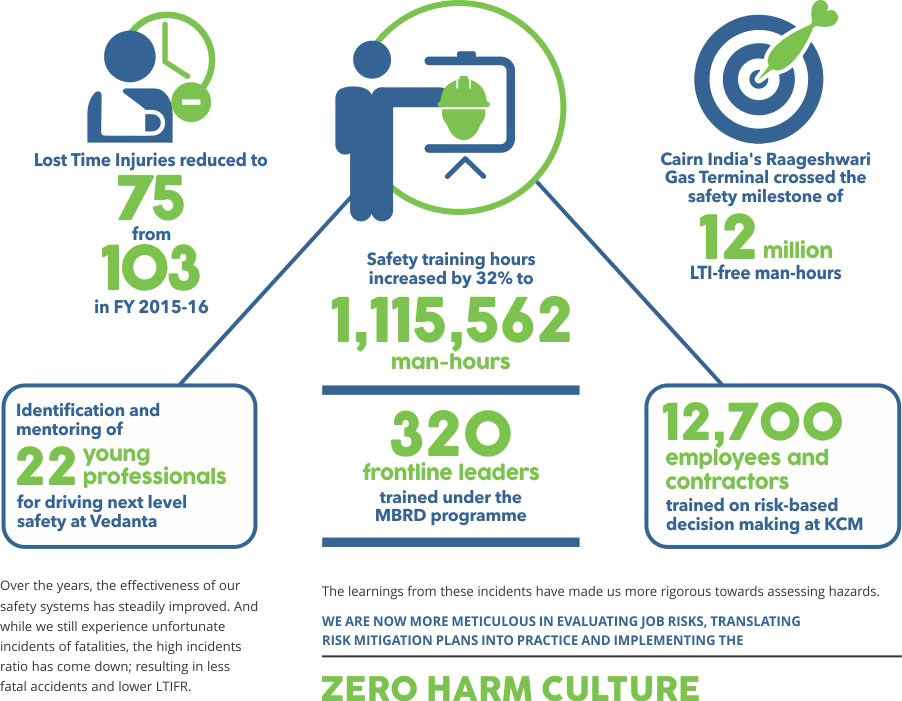
ZERO HARM CULTURE
We believe that all injuries are preventable. Creating and maintaining a Zero Harm Culture is our aim as well as our call to action. To translate this vision into an effective safety strategy, we have a comprehensive HSE policy in place. The goal is to embed safety as a value and the task is helmed by our senior management.
Our Chairman as well as our CEO fiercely advocate Zero Harm Culture by personally engaging with employees on a regular basis and deliberating the safety improvement opportunities. Our senior management takes responsibility for leading our safety strategy and communicating it across the workforce.
SAFETY & OCCUPATIONAL HEALTH ARE ONE OF THE CORE AREAS OF DISCUSSION DURING EVERY
VIRTUAL TOWN HALL MEETING CONDUCTED BY OUR CHAIRMAN, MR. ANIL AGARWAL.
For a culture of safety to gain permanence, it needs to permeate across every level of the organisation. This year, we continued to enthuse, educate and encourage every member of our workforce to embrace safety wholeheartedly as a value and line managers were made accountable for that. Safety & Occupational Health is a mandatory module in our induction and refresher training programme and periodic workshops are conducted to enhance safety awareness and knowledge among employees and contractors.
IN ORDER TO MAKE SAFETY A 'MUST HAVE' INSTEAD OF A 'GOOD TO HAVE', WE HAVE DIRECTLY
LINKED EMPLOYEE REMUNERATION TO THE PROGRESS ON IMPLEMENTATION OF SAFETY
PERFORMANCE STANDARDS AND PREVENTION OF FATALITIES.
Our Board-Level Sustainability Committee (chaired by the Board's senior independent director) and our Executive Committee (chaired by our CEO) regularly review our safety performance and share recommendations. Safety & Occupational Health are prime elements of the Vedanta Sustainability Assurance Programme.
We have Health and Safety Committees across Group Companies. These committees comprising members from the management as well as unionised workforce operate at the company, unit and sub-unit level depending on the locations & businesses. These committees meet at regular intervals and ensure that the programmes work in accordance with our established Sustainable Development Model and Framework. In case of operations where unions have not been formed, we have set up a monthly meeting mechanism that involves principal contractor and sub-contractors to discuss specific HSE issues. 100% of our total workforce is represented in formal joint management-worker health and safety committee.
Health and safety topics are also covered in the formal agreements with trade union.
THERE IS BROAD CONSENSUS THAT EMPLOYEES AND THE UNION WILL SUPPORT OUR BUSINESS
IN CASCADING MEASURES AND INITIATIVES FOR IMPROVING PRODUCTION/PRODUCTIVITY, WORK
CULTURE, QUALITY & SAFETY.
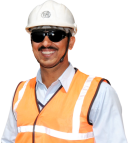
Implementation of safety performance standards |
![]() |
Last year, we initiated our first step towards elimination of critical hazards by identifying six types of them that account for approximately 75% of lost time incidents and grouped them under one common protocol: Group Safety Performance Standards.
The six critical areas identified were
WORK AT HEIGHT | ISOLATION | ELECTRICAL SAFETY | GROUND CONTROL | CONFINED SPACE ENTRY | VEHICLES &
DRIVING. THIS YEAR WE INITIATED A SEVENTH SAFETY PERFORMANCE STANDARD (SPS) ON CRANES AND LIFTING.
In addition to the six specific standards, we have two Technical Standards that govern Occupational Health Management and Safety Management in a broader context.
In the reporting year, focus was laid on the stringent implementation of SPS protocols across our businesses. The challenge was not only to introduce the safety standards but also to sustain them across the year.
We have made major progress towards embedding SPS across the businesses through rigorous training drives, monthly meetings, inclusion and ownership of top management into the safety assessment and mitigation, incorporation of safety alert mechanisms, interactive media, easy accessibility to HSE dashboards and metrics, deployment of safety materials and PPEs, regular communication between the management and workforce, and regular safety audits.
REAL-TIME INCIDENT REPORTING AT CAIRN (Oil and Gas Business)
We believe that there are two factors that differentiate us in the natural resources industry:
OUR HUMAN RESOURCES AND HOW WE LEVERAGE INNOVATION AND
TECHNOLOGY TO ENHANCE END PRODUCTIVITY.
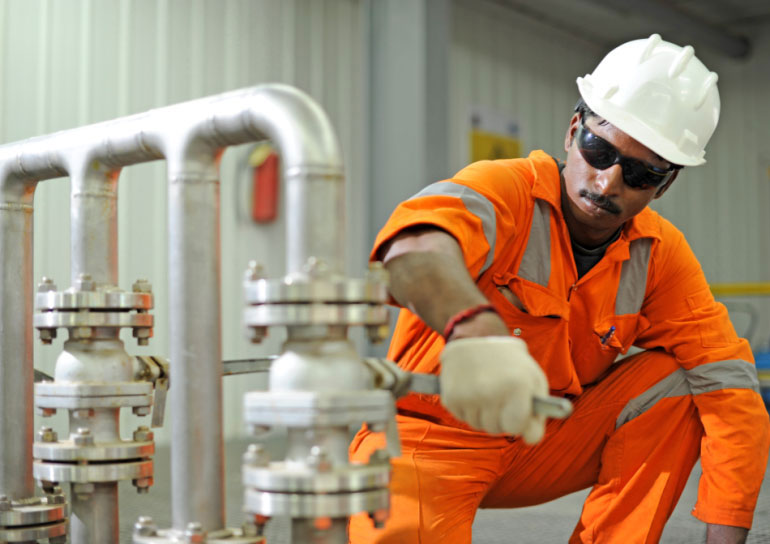
This year, we introduced a number of initiatives to embed technology into the safety management process.
Prime amongst these, is the online and real-time incident reporting mechanism we have in place. The LogChief, the digital Geological Logging Platform, helps us identify and ascertain any reportable incident before it takes a more catastrophic proportion. Data is made available to exploration & production managers in real time to enable efficient decision making and ensure immediate action and closure of any potentially hazardous situation. Work is also afoot to introduce a live safety dashboard that will be accessible across hierarchies - from line managers to the senior management team.
Our Safety Performance |
![]() |
We report our safety performance as per ICMM guidelines. We marked an overall declining trend in injury rates with the Group's Lost Time Injuries reducing from 103 in FY 2015-16 to 75 in FY 2016-17. With LTIFR of 0.39, FY 2016-17 ranks as our best year so far in terms of an overall safety performance.
At Vedanta, we believe that a healthy workforce is a more alert and productive one. To promote the overall well-being of the employees and as a precautionary measure, all our sites conduct Initial Medical Examinations (IME) and Periodical Medical Examinations (PME) for both permanent employees and contract workforce. We have also introduced capturing the injury statistics pertaining to the visitors and truck drivers etc., and initiated their medical examinations.
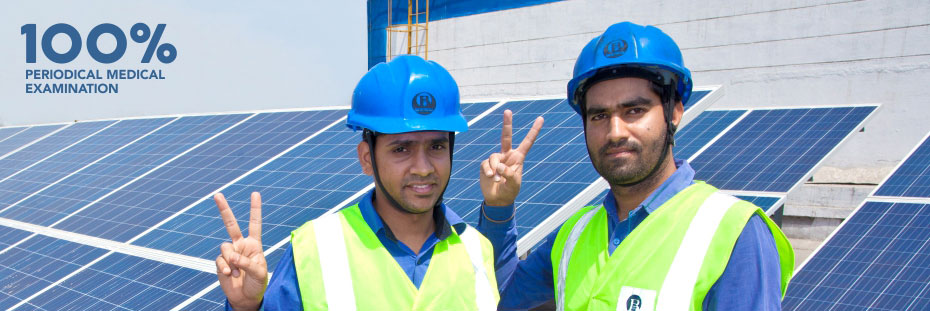
All our sites have a fully-operational and professionally manned Occupational Health Centres (OHCs). In addition to IME/PME for all our employees, the OHCs also provide facilities like first aid support, OPD facilities, and conduct various health camps to create awareness on health aspects and potential diseases.
Continuous work zone monitoring is carried out to ensure a safe and healthy workplace for the employees. Several initiatives like bag filters, dust monitoring, dust suppression, fugitive emission reduction, proper storage of hazardous chemicals/substances are incorporated to safeguard their health.
WE CONTINUE TO UPHOLD THE WASH PLEDGE BY PROVIDING ADEQUATE ACCESS TO SAFE DRINKING WATER AND
SANITATION FACILITIES TO OUR WORKFORCE ACROSS ALL SITES.
Apart from physical safety, we also undertake concentrated trainings on stress management and ergonomics to foster an environment of holistic employee well-being. All these interventions not only help in creating a clean workspace but also assist in maintaining the health of the employees. During the reporting period, we didn't observe any significant / major occupational diseases at our operating sites.
Although we succeeded in reducing the number of fatalities, it is still a performance that is unacceptable to us and is a matter of great concern and regret for the entire Vedanta group.
LTIFR
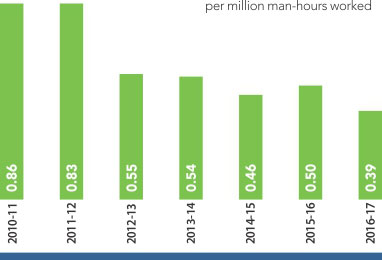
FATALITIES
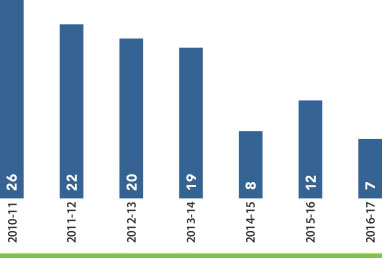
* In 2015-16, we revised our calculation definition in line with the revamped ICMM guidelines and reset the baseline. Thus, LTIFR for that year was revised from 0.46 to 0.50.
AN IN-DEPTH REVIEW OF EACH OF THESE INCIDENTS HAS BEEN CARRIED OUT TO ANALYSE WHAT WENT WRONG.
A Root Cause Analysis has been conducted by the top management of the respective businesses and the results
have been shared with the Board's Sustainability Committee to initiate appropriate action plans to prevent such incidents in future.
Incident Type | Prevention / Action |
Four third party contract workers were fatally injured from the collapse of a 250-ton crawler crane. | Reinforce our permitting systems and management oversight. Also rolled out seventh safety performance standard on Cranes & Lifting. |
One fatal accident each was related to blasting and working underground. | Effective reinforcement of safety performance standards for blasting procedures and underground safety have been ensured through regular monitoring. Reward and recognition initiatives have been carried out for increasing safety ownership among the employees. |
One fatal accident was related to vehicles and driving. | Strict adherence to the implementation of safety performance standards through periodic audits. Motivational reward and recognition programmes were initiated to cultivate safety accountability across the workforce. |
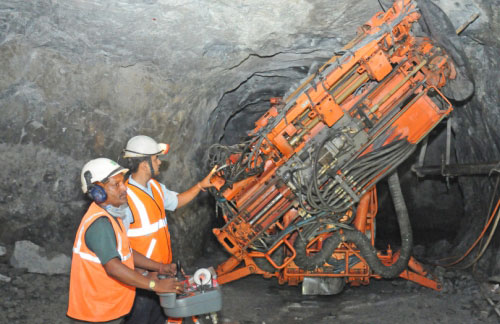
A high-potential (HIPO) incident is an incident or near-miss that, realistically, could have under other circumstances caused one or more catastrophic injuries. Awareness of HIPO incidents is a key factor in preventing them and we share the learnings of HIPOs to prevent their reoccurring at other sites.
During the year, we recorded a total of 117 HIPO incidents, with each fully investigated and the lessons
learned promoted across all businesses.
Institutionalising Zero Harm Culture | ![]() |
Best safety performance can only be achieved through precise execution of the safety practices and solutions. When one factors-in the dynamic work environment, safety improvement becomes a continuous process. Throughout the year, across business units and through a diversity of interventions, we pursued safety with rigour. Some of such initiatives are illustrated below:
Understanding the Risk
Identifying critical risks is imperative to strengthen risk-based decision making and to initiate remedial actions. Several identification exercises were carried out to have an in-depth understanding of the real challenges on ground.
PREVENTING FATALITY, SYSTEMATICALLY | HZL
The Fatality and Serious Incident Preventions Programme (FSIPP) commenced at HZL with an aim of dealing with critical risks, identifying their preventive measures and analysing the effectiveness of these mitigative steps. This initiative enables risk prioritisation and identification of barriers to eliminate them.
All smelters and mines have identified high risks and ranked the same to ensure safety
ownership.
Thus, accountability for managing risk through the barriers is defined. Periodic audits are conducted to monitor the robustness and adequacy of these barriers.
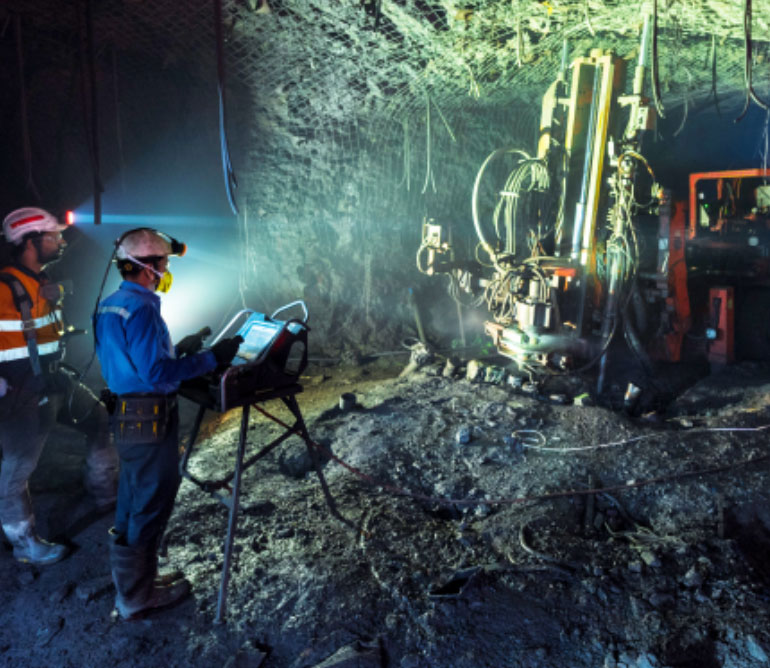
CASE STUDY |
DYNAMIC LEADERSHIP IN SAFETY ROLES
GROUP WIDE
Our Global HSE team comprises 365 professionals and, as an effort to promote leadership amongst HSE function, 22 dynamic leaders across the businesses were identified through a structured process for higher level of challenges and growth.
In these roles, they are being mentored by our leadership team and are provided with experience of being part of the various high level HSE - centric meetings. We envision that with the right guidance, these professionals will drive the next level of safety performance at Vedanta.
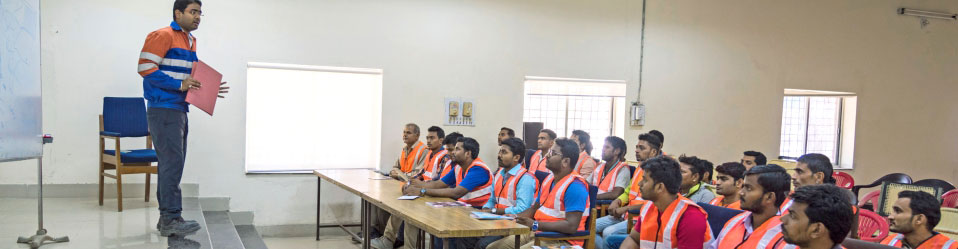
Here is what some of these 22 professionals say about
being part of this programme:
I AM THANKFUL TO THE HONORABLE CHAIRMAN AND THE
PANEL FOR EXPRESSING TRUST IN ME. I SHALL DELIVER MY
BEST TO ACHIEVE VEDANTA TARGET OF 'ZERO HARM, ZERO
WASTE AND ZERO DISCHARGE'.
SATHISH I A | AM, HZL

I REALLY APPRECIATE THE EFFORTS BEING TAKEN BY THE SENIOR MANAGEMENT TO SUPPORT AND ENHANCE THE POTENTIALS OF WOMEN EMPLOYEES IN THIS COMPANY AND I REALLY FEEL PROUD TO BE A PART OF IT.
SOMA BHARATI | AM, JHARSUGUDA

IT WAS A GREAT LEARNING EXPERIENCE FOR ME TO GO
THROUGH THIS EXCELLENT GROWTH WORKSHOP & FEEL
PROUD TO BE IDENTIFIED AS A LEADER.
KRUTISUNDER MOHAPATRA | AGM, JHARSUGUDA

THE EXPOSURE AND OPPORTUNITY TO ENGAGE WITH THE TOP LEADERS OF THE ORGANISATION WAS ITSELF AN EXPERIENCE OF A LIFETIME. THE FAITH YOU HAVE PLACED IN ME AND MY WORK MEANS A LOT TO ME, AND HAS GIVEN ME FURTHER IMPETUS TO PERFORM BETTER.
HARSHVARDHAN PANDE | AGM, JHARSUGUDA

Moreover 11 project teams consisting of members from diversified functions across the business has been assigned an objective related to 'HSE improvement' or 'HSE enabling' work streams.
These are:

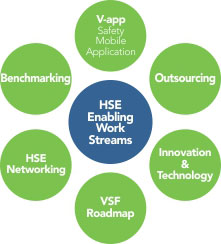
INITIATIVES
MAKING BETTER RISK DECISION (MBRD) PROGRAMME | GROUP WIDE
To enable cognitive solutions to the challenges, different sections of the workforce were empowered with knowledge through proper training based on their role and scope of operation. Last year, we piloted the MBRD programme - a combination of classroom and practical on-ground sessions, to empower line leaders to make better decisions by foreseeing the risks relevant to their routine and non-routine work profile, and understanding the consequences associated with these risks.
We have a structured review mechanism to ensure identification, analysis, mitigation and monitoring of safety risks on a continual basis. Our key areas of risk and their mitigation levers can be summarised as follows:
Type 1 Controls
Task Based
(leadership focus)
Job Safety Analysis
Safe Work Procedures
Task Hazard Assessment
Task Planning
Safety Interactions
Type 2 Controls
System Based
(process focus)
Standards
Golden Rules
Implementation Audits
Improvement Plans
Type 3 Controls
Business/System
(critical event focus)
Formal Risk Assessment
Bow Tie Analysis
Critical Controls
DURING THE REPORTING PERIOD, 320 FRONTLINE LEADERS ACROSS THE BUSINESS WERE TRAINED UNDER MBRD PROGRAMME. WE AIM TO EXTEND MBRD TRAINING TO 50% OF EMPLOYEES ACROSS ALL BUSINESSES BY 2020.
GEARING UP FOR ZERO HARM | GROUP WIDE
Once we identify the risks, the next logical step is to mitigate them through stronger processes, effective training and better safety mechanisms.
Major impetus was also given to awards and other motivational campaigns for sustaining these best practices and mitigative measures throughout the year. This included instant awards for recognition of best practices on a weekly basis, and longer term awards like 'best employee of the month' and 'best kaizen initiative' etc.
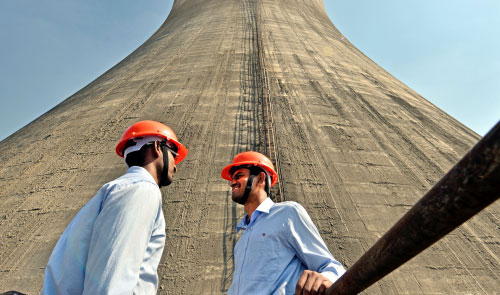
IDENTIFYING RISK TO CONTROL THEM BETTER | GROUP WIDE
Through constant all-inclusive engagements at every level of the organisation, we strive to achieve higher benchmarks of safety. Our Experience Based Quantification (EBQ) workshop on 'Pot Open Circuit' was held at Jharsuguda, which was chaired by Mr. Phillip Turner (Group Head-HSE) and was attended by seven technical heads from across Vedanta Limited. EBQ Workshops were also held on 'High PM Emission' and 'Pot line FTP Stack emission' which saw participation of employees from BALCO, Lanjigarh, Sterlite Copper, TSPL and Jharsuguda. Bow-Tie Analysis was carried out in each of these workshops for identifying the critical control measures to facilitate improved safety performance.
MULTIPLE STEPS TOWARDS SAFETY | BALCO
To reinforce safety ownership in our culture, a comprehensive safety training programme – Jagriti, was conducted at CPP 540 MW of BALCO.
The module is designed to create awareness on site safety requirements specific to the usage of gas cylinders, PPE and various other safety systems and provide practical demonstration on the safety requirements of these appliances. This resulted in greater knowledge of the machines among the workers who handle them.
The entire module has been derived from the Safety Training Module of IHS, Chattisgarh Govt. to ensure adherence to Govt. safety standards.
The training was attended by both senior management and workers and provided a shared platform for interaction on safety practices improvement.
More than 500 workers from Regular, Shutdown and Project area participated.
Additionally, during the reporting period, BALCO introduced a number of measures and initiatives towards enhancing safety:
A District Level Safety workshop was conducted in August 2016 involving all the industries of Korba & Champa region. A total of 55 delegates attended and shared safety best practices.
A Sustainability Vendor's Meet was organised in July 2016 in which around 40 vendors & suppliers were updated about Vedanta Sustainability Framework and Safety Performance Standards.
BALCO sustainability mobile app was launched for reporting environment and safety related incidents, positive acts, standards and policies etc. Closure of hazards also can be done through the app.
To ensure that the safety practices don't get lost in translation, the Dupont e-learning safety modules were launched in Hindi for workmen & contract workers.
Monthly safety motivational programmes are conducted for involving outsourced workers. Awareness events and competitions organised for driving safety and rewards were given to Best Safety Conscious Employees.
TOWARDS A SAFETY CULTURE | HZL
A host of initiatives and measures were introduced and carried forward at HZL to instil a culture of safety:
A Safety Training Park was set up at HZL to ensure reliable safety induction training and to provide a credible plant equipment safety experience before entering the plant.
Safety perception surveys were conducted to measure the effectiveness of the safety initiatives undertaken.
Rescue Refresher Training is held with the help of RRRT centre under which 4 sessions are conducted every month.
Safety stand downs were hosted at all units by site leaders to discuss and share the observations and learnings of the LTI/HIPO occurrences every quarter.
Safety town hall meetings were organised to facilitate live interaction between the senior management and 2,000 employees including contract workers and new hires.
DRIVING SAFE | GROUP WIDE
Our remotely located sites, involve extensive amount of driving. Considering the fact that we had a driving related fatality this year, special emphasis was given to ensuring driver safety by various businesses.
Safety Kiosks were installed in the HZL plant at prime driver locations to train the transport drivers about do's and dont's of driving. The kiosks made training more accessible and accelerated the safety induction process to ensure timely deployment of qualified drivers. The kiosks make the safety training more accessible and flexible, expedite the safety induction process and ensure faster deployment of qualified drivers on the road. Sesa Iron Ore in association with Institute of Road Traffic Education (IRTE), introduced a training programme on Defensive Driving for truck drivers who are engaged in the transportation of Iron Ore. The assessment of tests conducted for the drivers prior to and after the training confirmed that there was considerable enhancement in the drivers' knowledge and perception about road safety.
Our HZL plant has set up an in-house store for the purpose of renting Personal Protective Equipments to the drivers. The safety stores have been very effective in encouraging drivers, both new and old, to take and use standard PPEs in the plant.
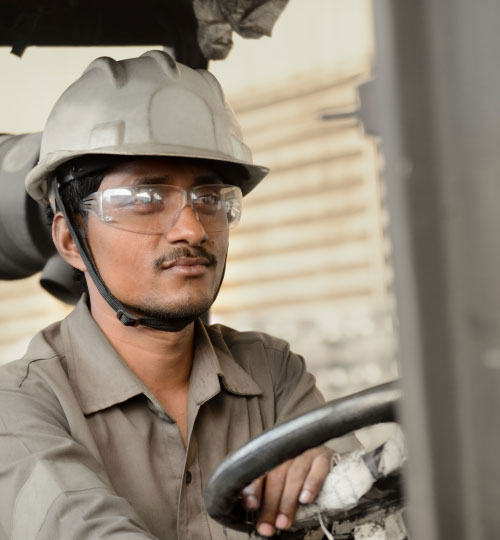
LIFTING RIGHT | STERLITE COPPER
Single Point Accountability (SPA) is one of the driving forces of safety management systems at Sterlite. Among our SPA protocols, 'Lifting Tools and Tackles' is a unique SPA, with greater emphasis on safe rigging practices, and proper usage of appropriate tools and tackles.
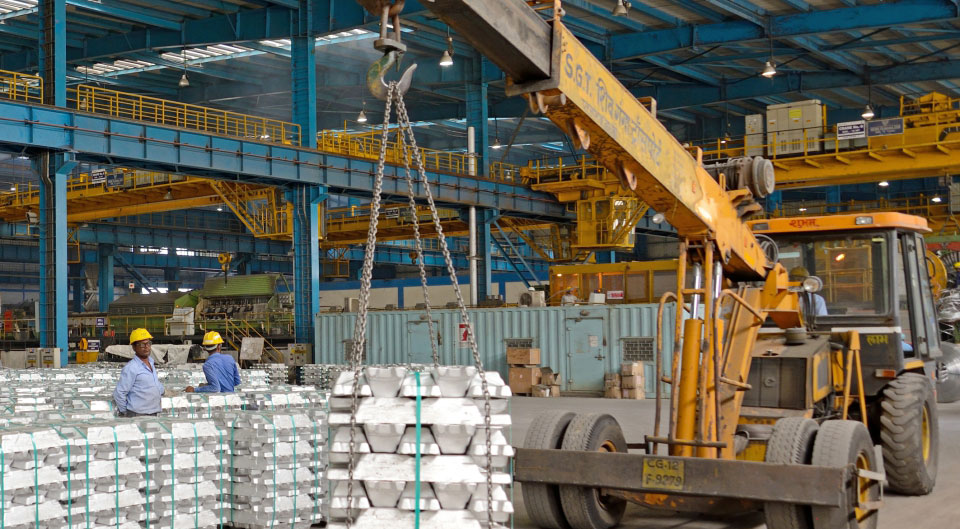
CASE STUDY |
CHINGILILA PROGRAMME
CHINGILILA PROGRAMME
IN ORDER TO STRENGTHEN ZERO HARM CULTURE AND IN RESPONSE TO SERIOUS ACCIDENTS, THE CHINGILILA PROGRAMME WAS INTRODUCED IN KCM IN SEPTEMBER 2014. CHINGILILA IS A BEMBA WORD MEANING 'PROTECT' - AN APT SAFETY MESSAGE.
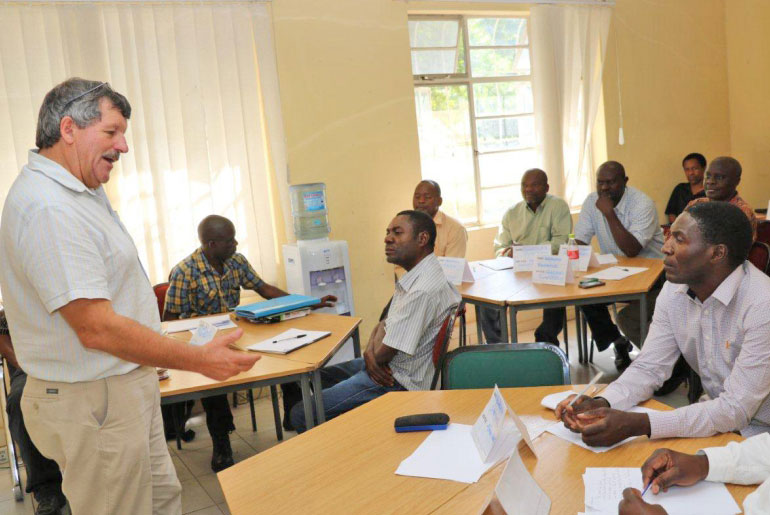
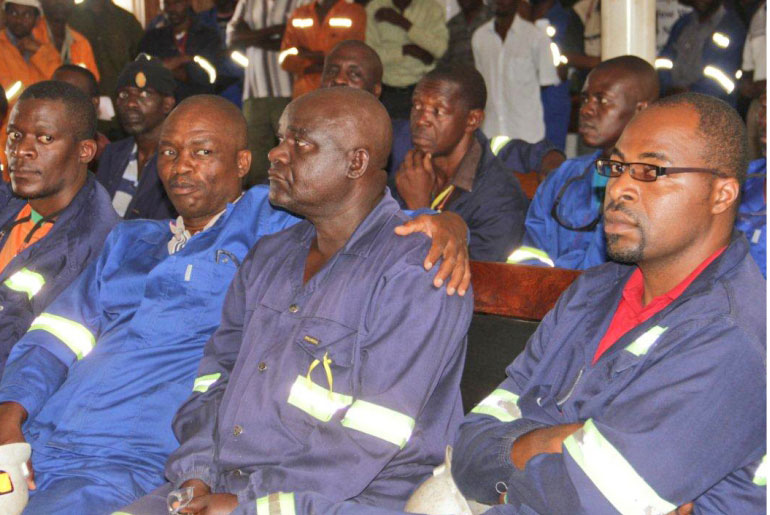
During the reporting period, to strengthen the mission to protect, a six-month intensive and holistic programme was introduced, under which
25 | Mine Captains |
designated as safety champions were instructed to regularly visit every working area to improve the safety awareness at the site and workplaces.
In parallel, a customised safety 'train the trainer' programme was developed for different levels of employees, supervisors, managers and executives. In a period of 2 months, a total of
148 | KCM employees |
(mostly production staff) were trained to become safety trainers. This team of trainers then trained around
12,700 | employees and contractors |
on risk-based decision making.
The Chingilila programme goes beyond imparting training. Following initiatives are testament of the holistic nature of the programme:
112 KCM safety procedures have been revised to incorporate risk assessment principles in all the safety procedures.
Ten Cardinal Rules of Safety have been introduced to highlight the ten primary risks at KCM.
The role of the safety department was restructured to focus on coaching of supervisors on safety issues. With the assistance of the senior management at KCM, the purview of safety department was extended to managing the cost audits with the assistance of senior managers.
An internal auditing course to empower managers in effectively handling the safety issues at their respective workplace.
A dedicated safety investigation unit has been established to ensure that all safety incidents and accidents can be investigated with greater focus on prevention strategies.
The design and implementation of the Chingilila Safety System at KCM has triggered significant improvements in the safety performance and has fast-tracked progress towards our Zero Harm vision.
|
FOR SAFETY TO BE 100%, IT HAS TO BE HOLISTIC. OUR SAFETY PROTOCOLS, BENCHMARKED AGAINST INTERNATIONAL STANDARDS, ARE CASCADED TO ALL OUR VERTICALS THROUGH REGULAR TRAINING INITIATIVES.
A series of comprehensive longer-term safety and health drives were conducted to further foster a work of safety ownership.
INITIATIVES
BEING SAFE | HZL
Safety to us is not just an act of compliance or a response to fears, it is a preferred practice and operations philosphy. At HZL, a unique initiative 'Being Safe' was designed with focus on reducing stress and cultivating a sense of responsibility towards safety practices among contract employees at the workplaces, and was also extended to the families of employees. To embed a culture of being safe, this intervention inspires holistic well-being of the employees through regular safety messages, safety specific movie screening, interactive discussions on values of life and meditative sessions. In all,
11 such drives were conducted by HZL's coporate communications team which reached out to
1,500 | employees, families and children. |
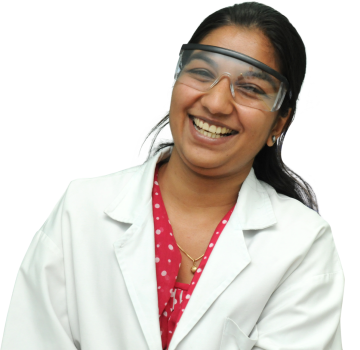
Road Ahead
At Vedanta, achieving and maintaining the Zero Harm goal remains our eventual aim. We intend to approach this goal through following means:
Transformation of HSE by leveraging our professional strength. We envision that the 22 high potential professionals spearheading the 11 work stream projects will take the safety culture of Vedanta to the next level.
Rigorously implementing safety performance standards to achieve a minimum 85% compliance across our businesses. We aim to attain 100% adherence in the future.
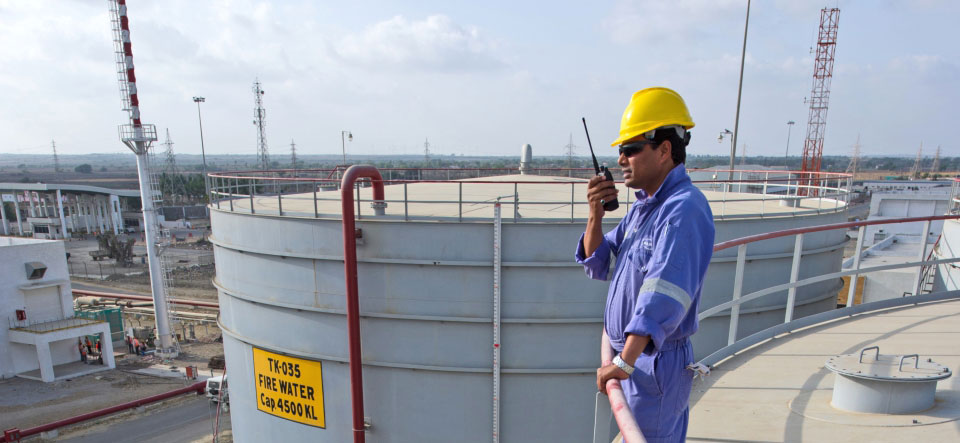
Taking forward the Leadership Safety Programme by
![]() |
Extending MBRD to 50% employees from each of our businesses to facilitate line leaders in making better decisions |
![]() |
Carrying out comprehensive assessment on all identified critical risk through Event Based Quantification (EBQ) |
![]() |
Performing baseline exposure assessments to potential health hazards across the businesses. |
Vedanta Safety Film (BALCO)