|
|
|
|
|
For a large part of business history, companies dealt with suppliers/vendors as external agencies. Their concerns were restricted to on-time and cost efficient deliveries. |
|
|
Soon the carbon footprint of the supplier started to stain end products, poor working conditions at the vendor end impacted businesses and malpractices caused companies who did business with them to face consequences. |
|
|
What ensued was unsustainable relationships. |
|
|
 |
|
|
A company is only as green as the supplier
it engages with. The automotive global supply chain touches nearly every other industry, including steel, plastics, textiles, electronics, and more. |
|
|
|
|
At Mahindra around 90% of the assemblies required for the manufacture of our vehicles are procured from suppliers. |
|
|
|
|
Hence, there is a compelling business case for us to engage with suppliers in jointly developing products and services which are commercially viable, preserve our environmental resources and look after our workforce and communities. |
|
|
SUSTAINABLE SUPPLY CHAIN |
|
|
|
|
|
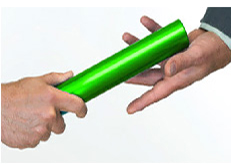 |
|
As one of the forerunners in following sustainable business practices, conscious efforts were made to extend our sustainable practices to our suppliers. Our Auto Sector (Nashik) and Farm Equipment Sector took up the challenge on this front. |
|
The emphasis has shifted from the 'green consumer' to the 'responsible retailer' whereby the supplier/service provider and the brand owner assume responsibility for ensuring that consumers can buy products and services with confidence in their source and manufacture. |
|
|
|
|
|
|
A challenge it indeed was since the suppliers at AS, Nashik were not very receptive to the idea of changing the way they worked, their main apprehension being increased cost in bringing about any change. |
|
AS, Nashik realized that this was a sensitive issue and dealing with it would require engaging at a deeper level with suppliers. They therefore initiated a supplier partnership drive called 'Partnership with suppliers for continuous improvement'. |
|
Gains were made by working closely with suppliers to identify focus areas of improvement in labour standards and environmental performance. |
|
The drive began with a program on 'Knowledge and best practice sharing with suppliers for fostering an environment for sustainable development'. |
|
The following were key components of this program: |
|
Groundwork |
As part of the groundwork, a detailed questionnaire for understanding the current process, and level of understanding of the environmental challenges, such as effects of irresponsible waste disposal etc. was sent to all suppliers. |
|
Prioritization |
The groundwork helped them prioritize suppliers in the following categories: |
|
|
Suppliers under categories A and B were taken on priority for the Continuous improvement program. |
|
Awareness |
Focused awareness sessions on environment, health & safety issues and the importance of green supply chain was first undertaken for the identified suppliers. |
|
Training |
Programs on importance of green supply chain and EHS Management system development were conducted. Realizing that cost was indeed an issue with small suppliers, Green SCM Clusters were formed and one consultant was appointed to guide the cluster to adopt sustainable practices. Training facilities/infrastructure was provided by M&M. This made the initiative affordable for these small scale units. |
|
Audit |
The company's Auditors were trained to conduct environment/EHS related audits at these supplier facilities and audit check sheet prepared to ensure comprehensive audits. Physical audits were also conducted at suppliers' facilities and legal audits conducted at 35 tier 2 suppliers through consultants. |
|
Corrective Action |
Plans arising out of the above audit reports were drawn and corrective action plans executed. |
|
Impact |
|
|
These impacts were seen within 12-15 months of initiating the Supplier partnership drive.
Some initiatives with the 2nd tier suppliers have also been started. Due to the positive results
it is proposed to strengthen the process and initiate further interventions with primary suppliers as well as the 2nd tier suppliers. |
|
|
|
AS, Nashik realised that they needed to be sensitive to the financial and non financial constraints of their suppliers and needed to structure programs keeping these sensitivities in mind. This initiative has resulted in a marked improvement in its supplier relationship. |
|
|
|
|
|
|
|
|
|
|
FES has its presence in around 25 countries across six continents with more than 1000 dealers world-wide. In this challenging environment it was necessary to upgrade supplier competencies so as to be able to consistently provide quality products at competitive cost to customers. |
|
Two years ago FES had established the Mahindra Yellow Belt (MYB) QC approach to problem solving as a proven methodology, employing QC Tools to solve chronic quality problems. This approach has now been extended to suppliers as well and was introduced in a program on 'Awareness and capacity building for enabling suppliers to build a Sustainable enterprise'. |
|
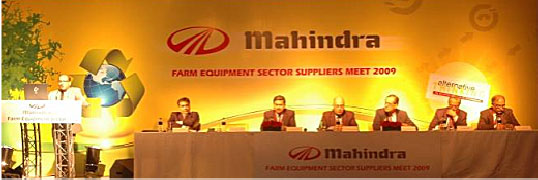 |
|
This year, 13 Business Partners showed keen interest in implementing this methodology in their respective organization. 15 Participants were nominated for the MYB - Business Partners Training Program - an action oriented training program, wherein the participants undergo two days of training, followed by an objective test, and thereafter apply the learning in a Project Problem selected by them and approved by Mahindra & Mahindra. |
|
During the year, two MYB- Business Partners Training programs have already been organized. The response for MYB from the participants was very encouraging; and the overall rating of the Training program was 4.45 on the scale of 5. |
|
Impact |
|
|
 |
Better integration of Sustainability strategy in the FES supply chain. |
|
|
 |
Sustainability is no longer limited to Mahindra & Mahindra and has percolated to external stakeholders as well. |
|
|
|
|
Suppliers are keen on improving their work standards irrespective of their economic status, as they see great value in such engagements. Moreover, these initiatives are actually perceived as incentives by the suppliers and negate the myth that all suppliers work only for financial incentives. |
|
|
Such alternative engagements will help enhance Mahindra's brand reputation, provide
operational benefits, help enhance profitability, ensure environmental protection and mitigate potential social risks. |
|
|
|
|
|
|
|
|
|
|