|
|
|
|
Innovation is nothing but a new
idea put into action. |
|
|
And most of such innovations that have the power to empower corporate growth aren’t discovered in the lab, or in the isolation of the executive suite. |
|
|
They come from the people who daily fight
the company's battles, who serve the customers, explore new markets and fend off the competition. Unfortunately, many a time organisations that aspire to lead by innovation fail to explore a diverse array of new ideas. |
|
|
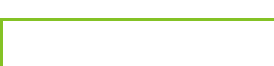 |
|
|
The only way to get great ideas is to get lots of ideas from lots of people. |
|
|
|
|
At Mahindra therefore an emerging trend is that
of converging minds - right from the shop floor to board room - to generate ideas that can expedite innovation and enhance business performance. |
|
|
|
|
We do this, because we believe that no idea is too small to be left unheard. Through the implementation of Ingenious Drive, we encourage workmen to ignite ideas and increase their involvement in improvement projects. |
|
|
WORKMEN INVOLVEMENT IN IMPROVEMENT
PROJECTS THROUGH i4 TEAMS |
|
|
|
|
|
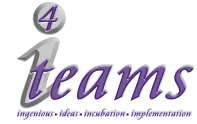 |
Mahindra and Mahindra - Limited Automotive Sector rolled out 'Ingenious Drive' in 2004 to further enhance the Customer Centricity. The Promise Statement was also unveiled aiming at unleashing the passion of its people to surpass the latent desires of customers. In first phase, only executives were made aware about the Ingenious Drive and Promise. In phase - II the workmen were also made aware of the same. This drive was focused on making the organization, an idea-led organization, where everyone - from the board room to the shop floor - were involved in generating ideas. |
|
|
To tap immense potential of its workmen and to increase the employee involvement in improving the plant performance, improvement teams had been formed across Auto Sector production units as a part of Ingenious Drive. These teams, christened as "i4 teams" are natural working groups led by an officer and generate ingenious ideas to make differences at their own level, to bring improvements in areas of productivity (P), quality (Q), cost (C), delivery (D), safety (S), morale (M) and product features. Today, all workmen across the Auto Sector are members of i4 teams. |
|
|
|
The ideas generated revolve
around efforts to: |
 |
Increase production & productivity |
|
|
 |
Conserve energy |
|
|
 |
Reduce cost by better methods |
|
|
 |
Eliminate waste or cost control |
|
|
 |
Improve quality |
|
|
 |
Remove bottlenecks |
|
|
 |
Increase safety & prevent accidents |
|
|
 |
Better housekeeping |
|
|
 |
Improve the environment |
|
|
|
Financial Year - April to March |
|
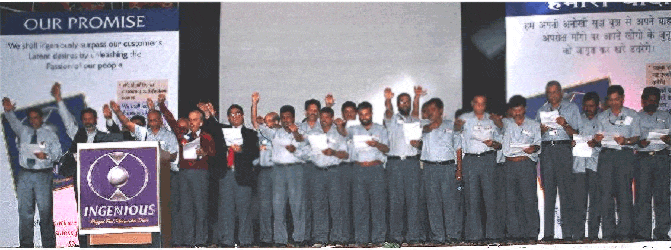 |
|
|
THE IDEATION PROCESS |
|
The i4 teams, formed mostly from the group of workers on the same line,
are led by an officer. During the meet held at least once every month: |
|
 |
Each team brainstorms for an hour |
 |
PQCDSM related ideas are recorded on the i4 Suggestion form |
 |
Accepted ideas are implemented with help of concerned dept / team. |
 |
Action plan for pending ideas are discussed. |
|
|
Annual competitions are held where winning teams are recognised and awarded. The team members are also awarded different i-Points for ideas submitted, feasible ideas and ideas implemented. Each point is equal to INR 1, and can be redeemed by workmen every quarter for attractive gift vouchers. |
|
The i4 teams have been highly successful at all locations, generating and implementing thousands of ideas across the Sector. |
|
|
|
|
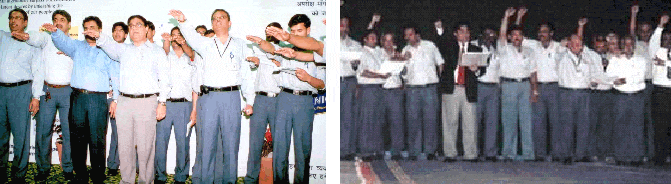 |
|
|
RESULTS |
|
These ideas are increasing productivity across plants, improving quality, delivering safety, improving morale and generating savings. |
|
Another interesting facet of the i4 concept is the active sharing among plants, whereby teams from each plant visit each other to share insights and offer suggestions. This cross learning created by the i4 concept is fertile ground for new ideas. |
|
|
|
|
|
|
|
|
|