|
|
|
|
Growth is good. |
Yet investments in growth are invading sensitive eco zones, relocating natives to alien lands, and sowing the seeds of inequitable progress. |
|
|
While investors continue to dissolve responsibility beyond the financial bottom line. |
|
|
Returns from such investments will only draw a blank for future generations. |
|
|
 |
|
|
All good investments are those that give lasting sustainable returns. |
|
|
|
|
At Mahindra we believe that the quantum of
black in the bottom-line is directly proportional to the quantum of green in the manufacturing line. |
|
|
|
|
We have therefore made a large investment in making a greener, cleaner and profitable tomorrow possible by setting up a state-of-the-art plant at Chakan with a host of alternative initiatives. |
|
|
GREEN FACTORY AT CHAKAN |
|
|
|
|
|
The Chakan plant has been designed as a fully integrated facility for multiple platforms - from press to body to paint to General Assembly and the aggregates all coming up simultaneously. |
|
At the plant, a cluster of 70 solar dishes will tap the sun's energy to cut CO2 emissions by 3,500 tonnes a year, all the while ensuring energy savings of 1.8 lakh units a year. |
|
Completed in a record time span of 22 months and envisioned as the hub of innovation and technology for the Mahindra Group, the auto manufacturing plant
at Chakan aims to set new benchmarks in automotive excellence. With a phased investment of approximately INR 50,000 million, this plant is spread across 700 acres. It has a manufacturing capacity of 3,00,000 vehicles per annum and is equipped to roll out multiple products ranging from a 0.75 tonne Maxximo to a
49 tonne Navistar truck. Our new SUV and Pickup range and product line for the
US market will also be manufactured at this facility. |
|
Green Highlights |
|
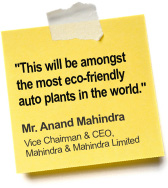 |
|
 |
|
Built as a green facility, the highlight here is that at each stage of the vehicle assembly, M&M has given cost efficiencies a
re-look through its green shades; be it harnessing the sun's energy to reduce LPG and electricity use, promising to transform the tough terrain of the plant in to a lush landscape, ensuring zero discharge or installing a HOC (Heat of Compression) dryer in place
of conventional electrical refrigerant dryer. |
|
A host of various such green initiatives will ensure an incremental reduction in energy consumption and CO2 emissions over the years. A projected estimate of energy savings and reduction of CO2 emissions for two years is as shown in the adjacent table. |
|
|
|
UNITS |
FY 2010 |
FY 2011 |
|
CO2 Emissions Reduction |
Tonnes |
3590 |
7600 |
|
Power Savings |
MWH |
3300 |
7000 |
|
Fuel Savings |
Tonnes |
330 |
700 |
|
|
|
|
|
|
|
|
Recycling of waste water through reverse osmosis and multiple effect evaporation will ensure zero discharge. In the future, plans are at place to reduce the fuel consumption through the installation of Plate & Tube Reverse Osmosis (PT-RO) system on RO reject and solar dish on existing MEE. |
|
|
|
A combination of chiller & closed loop cooling tower for press shop hydraulic cooling, closed loop cooling tower for all body shops and fanless cooling towers in utility ensures reduction in energy consumption and CO2 emissions. |
|
|
|
To increase the green cover in the vicinity we are aiming to plant approx. 7,000 trees across the location. To evade soil erosion and sediment control, black cotton soil generated during land grading was stored inside the plant and later mixed with red soil and used for gardening. |
|
|
|
|
|
|
|
Installation of hydro pneumatic system with variable frequency drive for water supply pumps to maintain the water supply pressure and reduce power consumption. |
|
|
|
Installation of HOC (Heat of Compression) dryers in place of conventional electrical refrigerated dryers and set up of centrifugal compressors with high tension efficient motors have resulted in improving the specific power consumption to 0.15 KW/CFM with estimated annual
savings of INR 25,00,000 in operating cost. |
|
|
|
The use of a cluster of 70 solar dishes will tap the sun's energy for eventual use in the chillers in the paint shop. Furthermore, photovoltaic panels will be used to power street lights in remote areas and conventional electric driven ventilation system will be replaced with natural turbine ventilators. |
|
|
|
|
|
|
|
|
Furthermore, the Chakan plant will not only provide an impetus to industrial growth in the region but will also present significant employment opportunities to local residents. Mahindra Chakan has around 1,400 employees at present. At full capacity, it will provide 5,000 direct jobs and five times as many indirect jobs. As a part of its initiatives to empower the local youth with employable skill sets, Mahindra has signed a Memorandum of Understanding (MOU) with the Government of Maharashtra for the development of two tribal Industrial Training Institutes (ITIs). The company has also allocated 71 acres for a vendor park. Six large suppliers have already set up base with place for another four. |
|
|
|
With its superior technological processes, large-scale manufacturing set up and eco-friendly focus, the plant is a paradigm of smart and sustainable engineering and a testimony to the Mahindra Group's far-reaching vision. |
|
|
|
|